SALIENT Project Completes 2 Year Milestone
SALIENT Project Partners outside the HQ of Fraunhofer IWU, in Chemnitz, Germany, on 17-18 September 2024
The SALIENT project recently celebrated its second anniversary, bringing partners together once again for a General Assembly meeting to discuss recent developments within this EU initiative aimed at reshaping the automotive sector. The meeting took place at the headquarters of Fraunhofer IWU in Chemnitz (Germany) on 17 and 18 September 2024.
The two-day meeting provided a valuable opportunity for consortium partners to share milestones achieved and plan the next steps for the final year of SALIENT.
The meeting started with an overview of the project’s global status presented by Mrs Denise García from CTAG, followed by a scientific and technical progress update delivered by Prof Ahmed Elmarakbi from the Northumbria University (UNN).
Let us review the accomplishments of each Work Package (WP) and how they will contribute to the creation of a Front End Structure (FES) made from lightweight materials, designed to enhance road safety and reduce injuries and fatalities.
Day 1
WP2: Structural Concepts Design and Optimisation
Dr Engy Ghoniem from the UNN, the leader of WP2, provided updates on the sustainability and economic assessment of SALIENT innovation. She discussed the findings of a comparative Life Cycle Assessment (LCA) between the FIAT baseline and the new SALIENT FES, made from Aluminium and Carbon Fiber Reinforced Polymer. The results highlight the potential benefits of these materials in the automotive industry, showing that while their production has higher environmental costs, their lightweight properties contribute to substantial fuel savings during the vehicle's operational phase.
Dr Ghoniem also presented the ongoing Life Cycle Cost (LCC) evaluation for aluminium and carbon fibre-reinforced polymer (CFRP) components. She explained that the assessment is being tailored based on advancements in prototyping, with a focus on energy and manpower costs. In line with SALIENT's environmental goals, using aluminium and carbon fibre is expected to significantly reduce fuel consumption during vehicle operation.
As a next step, WP2 activities will focus on refining LCA results, collecting inventory data for the baseline, calculating fuel consumption, and running simulations to evaluate the expected use phase based on vehicle lifespan and kilometres driven. Additional evaluations, including crash performance comparisons and techno-economic assessments, are also planned.
Weight Reduction Achieved in both BCFES & ACFES (Cidaut)
Mr Javier Romo García and Mr Jorge Velasco Manrique from Cidaut, the partner responsible for the analysis and multi-parameter design optimisation of the FES, explained how the hybrid bumper has been optimised by reinforcing the metallic bumper with UD CFRP tapes using Laser Assisted Tape Winding. Another achievement includes the finalisation of the crash box, which now incorporates aluminium adapters. Bonding and riveting have been selected as the primary joint technologies for attaching the crash box to the bumper beam and vertical supports, offering a robust yet lightweight solution. Significant weight reductions have been achieved in both the Bumper Crash Front End System (BCFES) and Advanced Crash Front End System (ACFES) components, with mass savings of 54.6% and 54.0%, respectively.
WP3: Innovations in Materials Development and Manufacturing Processes
Mr Sebastian Iwan from thermoPre ENGINEERING GmbH led this WP until its recent end in May 2024 (M21), presented the activities of optimised lightweight materials development, cost-effective manufacturing technologies, and the integration of smart embedded sensors. Following this, Mr İlyas Artunç Sari from ASAŞ Aluminium discussed the optimisation processes for Aluminium 6063 and Thermoplastic Carbon Fibre Reinforced Polymer (TP-CFRP), alongside a detailed techno-economic analysis comparing stamping and extrusion methods for cost, material savings, and productivity. Sandblasting and Vestamelt Hylink® powder priming were tested to enhance adhesion in hybrid materials. Additionally, ASAŞ explored 3D printing techniques, particularly Screw Extrusion Additive Manufacturing (SEAM), to assess the cost-effective production of complex parts for hybrid materials like aluminium and CFPA6. These efforts are advancing the SALIENT project’s goals of enhancing sustainability and performance in automotive applications.
Finally, Mr Matteo Basso from Fiat Research Centre (CRF) outlined the selection of joining technologies such as mechanical and adhesive bonding, welding, and riveting for vehicle component manufacturing. He highlighted the progress in induction welding technologies to enhance joining efficiency for thermoplastic composites. These technologies have now matured to a level suitable for the production of medium and small cars, such as the Fiat Panda model. Additionally, CRF developed a detailed assembly sequence aimed at implementing fully automated systems, significantly improving manufacturing efficiency and scalability. All these activities prioritise sustainability by focusing on the recyclability and reusability of components at the end of a vehicle’s lifecycle.
WP4: Industrial Feasibility and Deployment Demonstration
Mr Patryk Nossol, Mr Arham Saleem, and Mr Robert Meltke from Fraunhofer IWU presented an overview of WP4, where the FES concept will be manufactured and assembled to demonstrate industrial feasibility. They highlighted how the final materials and geometries were selected using AC1 (SMA wires located on the crash boxes) and shared technical 2D drawings of all aluminium parts and subassemblies with ASAŞ. Currently, the BCFES crash boxes have completed production and post-processing, and are ready to be shipped to Cidaut for further testing. Future steps include the production of an AC1 crash box. Risks and challenges were also discussed, noting the tight schedule for manufacturing, testing, and assembly. Mrs Friederike L. Kühl from Etelätär Innovation explained the activities planned for the economic analysis of the project, focusing on increasing production to medium-high volumes, evaluating industrial feasibility, and estimating costs per prototype. She also outlined plans for analysing future raw material pricing to enhance production efficiency and validate cost estimates.
WP5: Crash Analysis and Virtual Testing
FES Simulation and Optimisation (Virtual Vehicle Research GmbH)
Mr Karlheinz Kunter from Virtual Vehicle Research GmbH, the leading partner of WP5, provided an overview of the project and highlighted milestones achieved thus far. Mr Victor Garcia from Applus+ IDIADA presented activities focused on simulations and optimisations of FES components. These activities included simulations of three scenarios (turning, braking, and turning while braking) to evaluate the durability and fatigue performance of the FES. Maximum stress values were identified, with valid stress levels determined to be lower than those likely to induce fatigue. Further activities included geometrical optimisation of the BCFES based on energy absorption capabilities. Various active concepts, such as shape memory alloys (SMA) and tailored load paths, were also explored. Mr Kunter emphasised that further testing is needed to correlate with AC1. The next steps for WP5 involve refining load case scenarios, designing refinements, and implementing experimentally calibrated joint models.
WP6: Testing, Validation and Assessment
Mr Javier Romo and Mr Jorge Velasco from Cidaut, the leaders of WP6, explained how the activities initiated in the second year are focused on the initial testing and validation of components. In later stages, the activities will aim to define and execute a new testing protocol (in compliance with existing and future crash testing standards for certification) for crash and compatibility analysis. Currently, various tests on CFRP crash boxes and other components are ongoing, with outputs including acceleration signals, force measurements, and high-speed videos. Mr Victor Garcia from IDIADA elaborated on how validation will take place and assess compatibility as one of the future steps. Mrs Vanessa Ventosinos from GTAC explained how end-of-life scenarios for recycling and reuse will be evaluated, focusing on materials separation before recycling in collaboration with project partners CRF, FRA, tPE, and ASAŞ.
Day 2
Day 2 started with the presentation of two more ongoing WP packages:
WP7 Dissemination, Exploitation & Communication
Dr Aitor Hornés from BAX, the leader of WP7, provided an overview of the activities currently taking place and a timeline for upcoming tasks. He presented the Key Exploitable Results identified so far in collaboration with consortium partners and outlined the steps to be followed next. Later, Mrs Friederike L. Kühl from Etelätär Innovation gave a detailed presentation on Communication and Dissemination activities, which involve all consortium partners. She reviewed the outreach achieved by SALIENT so far and explained the necessary actions to be taken in the coming year to ensure the successful dissemination strategy of the project and maximise its outreach. Mr Victor Garcia from Applus IDIADA then explained the standardisation process and the analysis of the applicable standardisation landscape within SALIENT. He outlined the identification of regulation processes, including those related to frontal collision and frontal offset collision, using information derived from the largest markets. He also noted that the analysis will examine whether existing regulations have specific requirements regarding the deformation of front-end structures and identify any significant differences between them.
WP8 Management
Mrs Denise García from CTAG provided an overview of the overall project coordination, the general objectives, and the necessary next steps of the project. Prof Ahmed Elmarakbi from UNN followed by highlighting the scientific and technical management objectives. Mr Mateo Basso from CRF then gave an overview of the Quality and Risk Management, while Mr Patryk Nossol and Mr Arham Saleem from Fraunhofer IWU explained the Open Science and Data Management Plan. They also mentioned a recent workshop organised by Fraunhofer, which provided insights into the fundamentals and benefits of open data access and open research principles. Dr Ricardo del Valle from BAX highlighted the actions that need to be taken by the project partners by the end of the project and gave an overview of the exploitable results and the structure of the Innovation Board.
Finally, some closing remarks from CTAG and UNN marked the end of this two-day meeting.
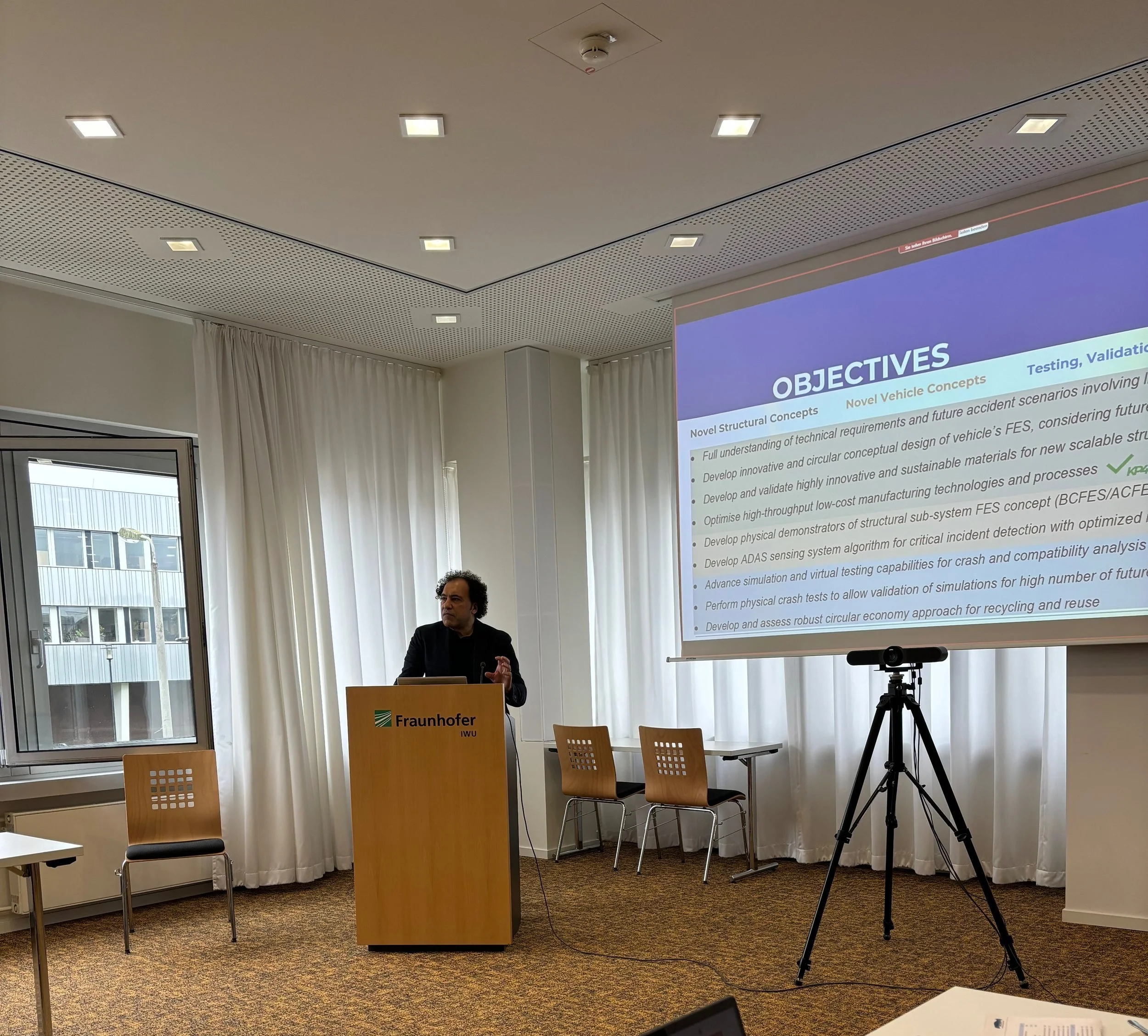
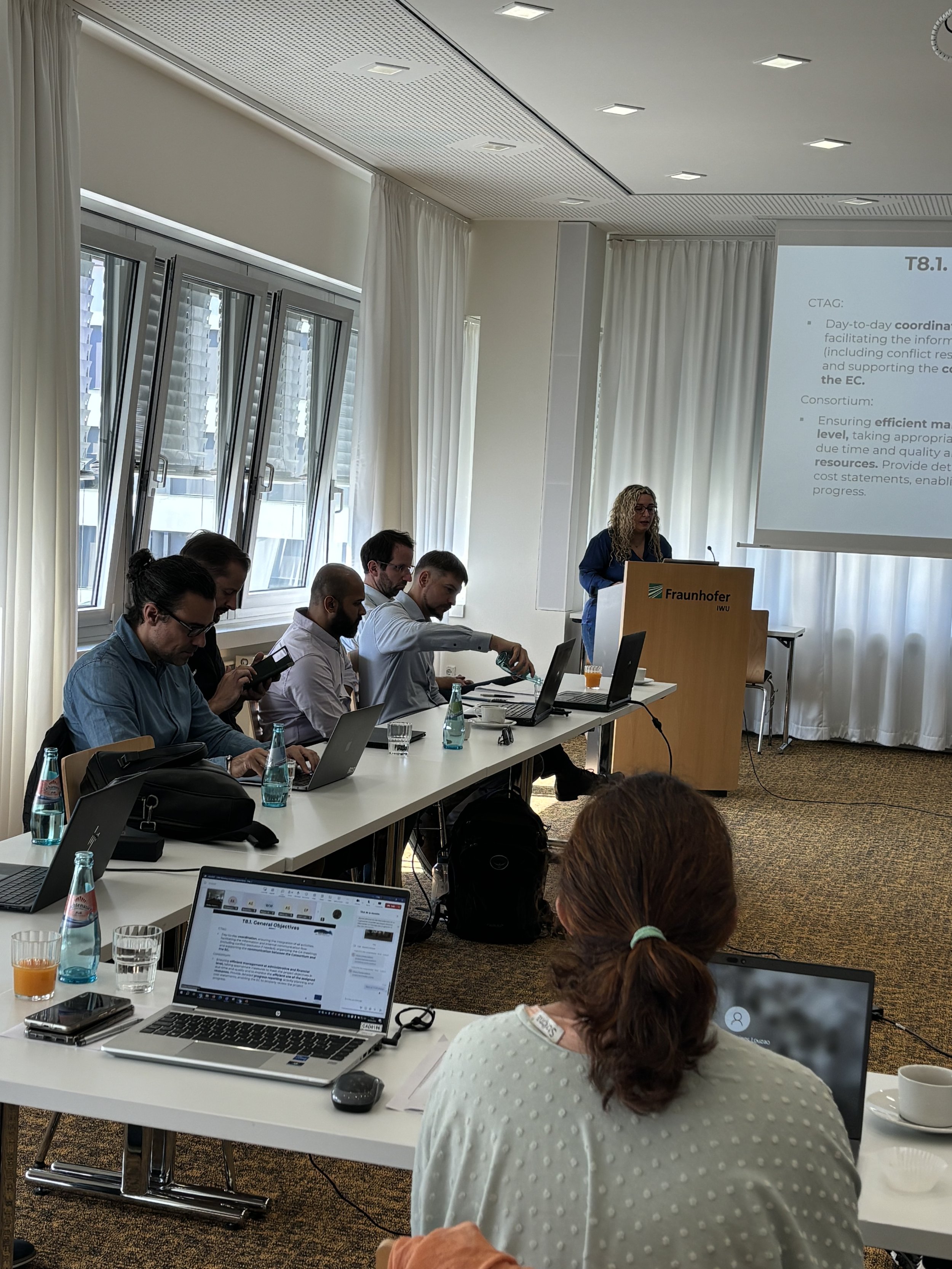
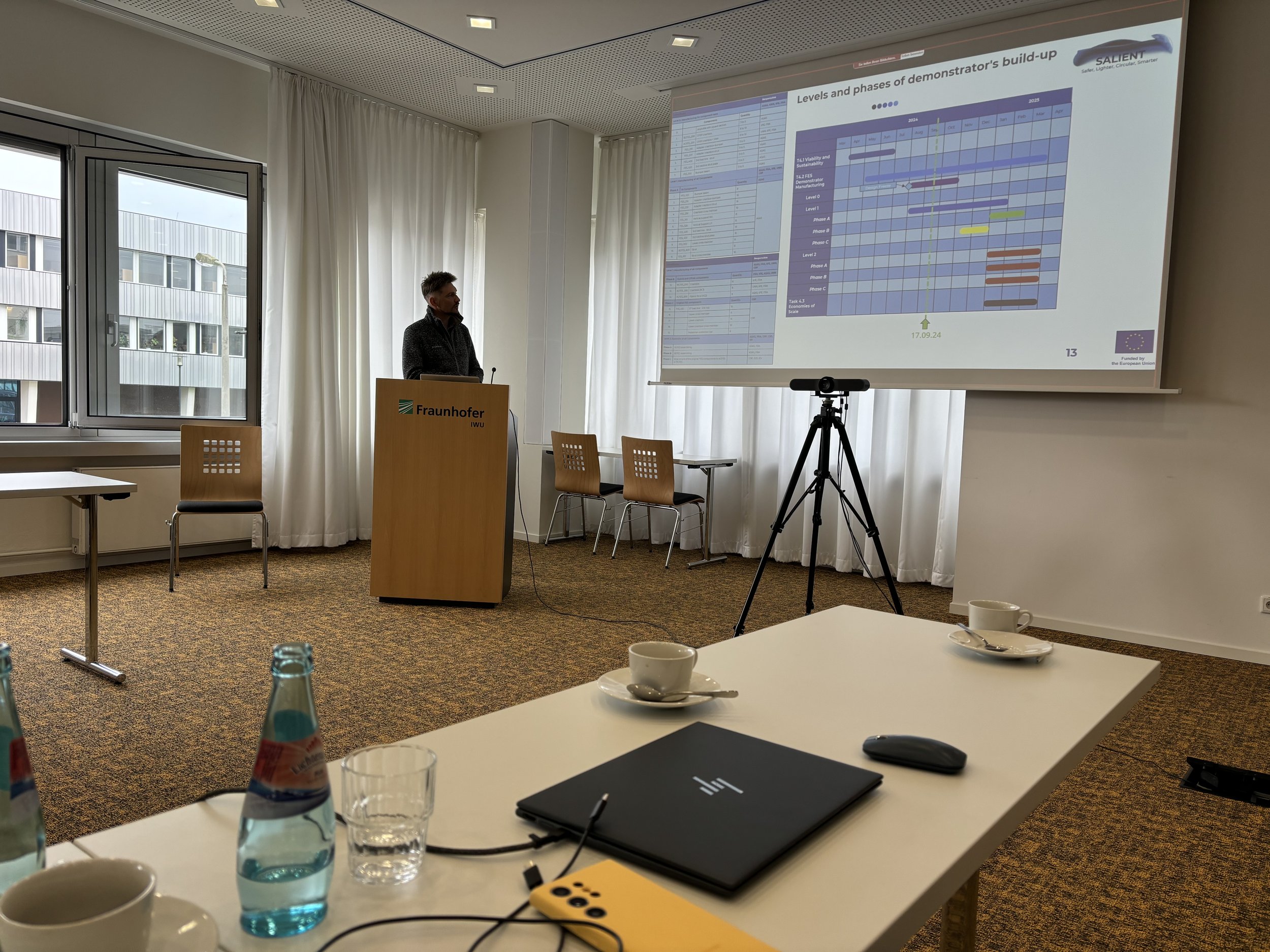

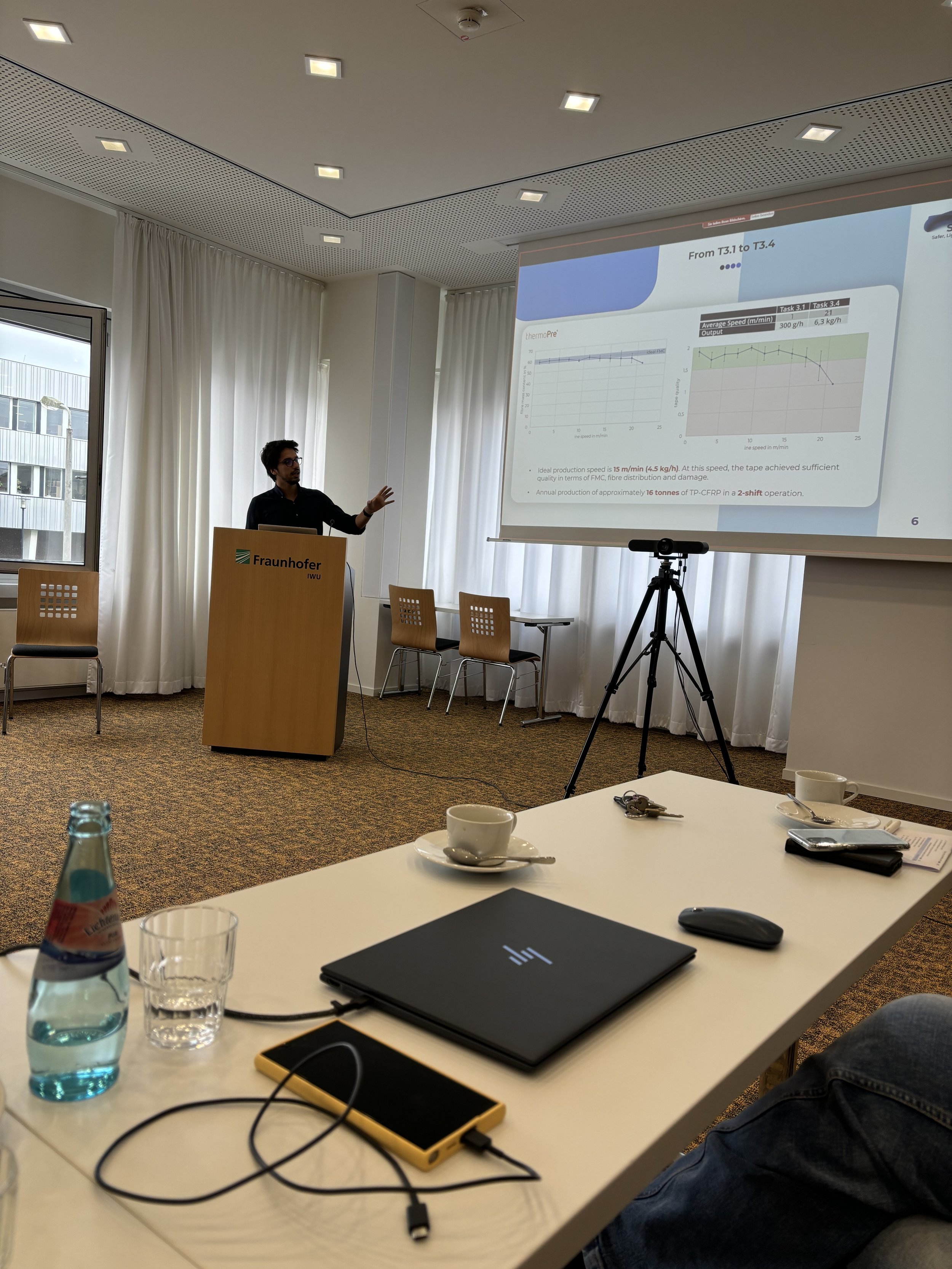
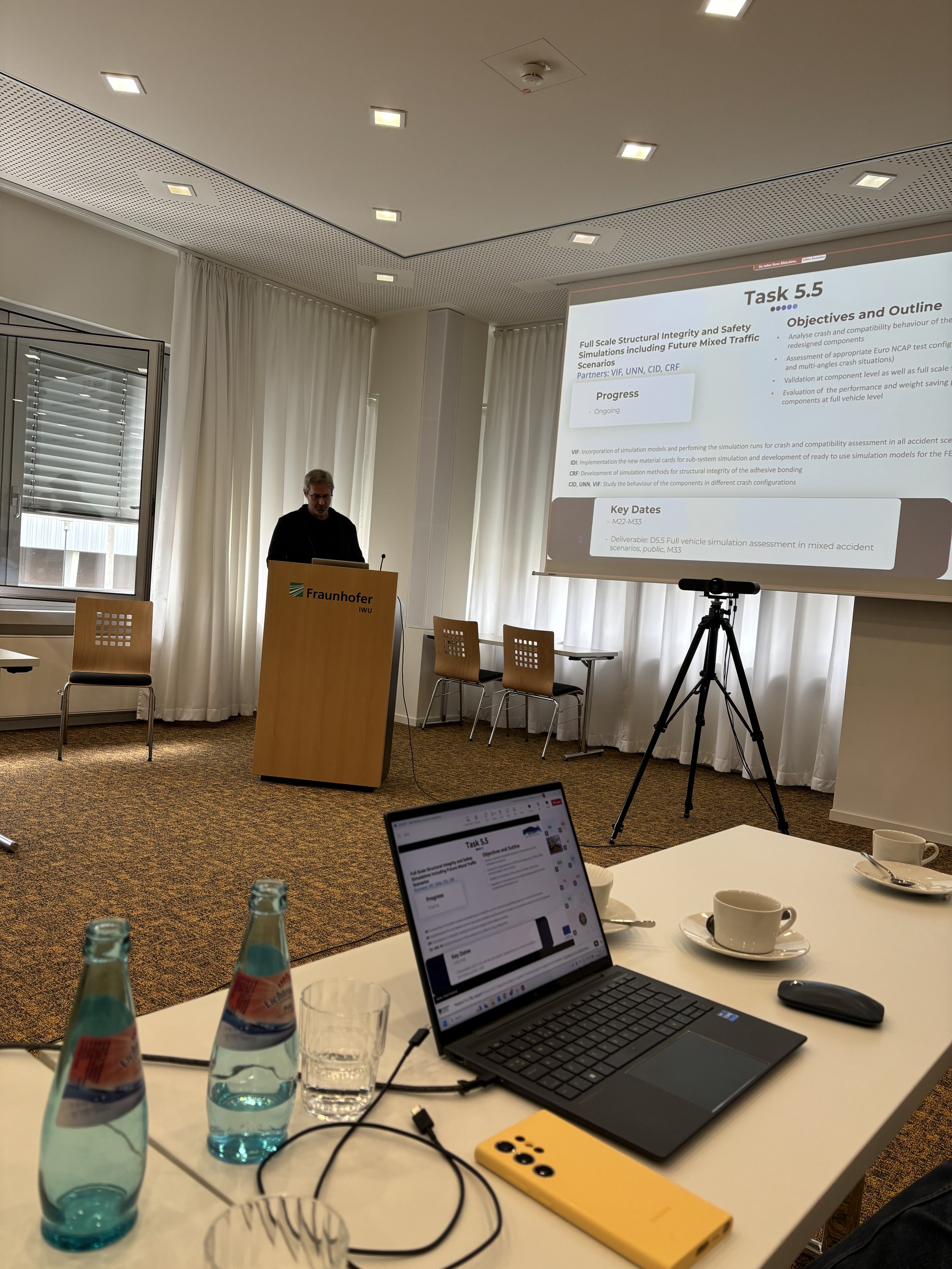
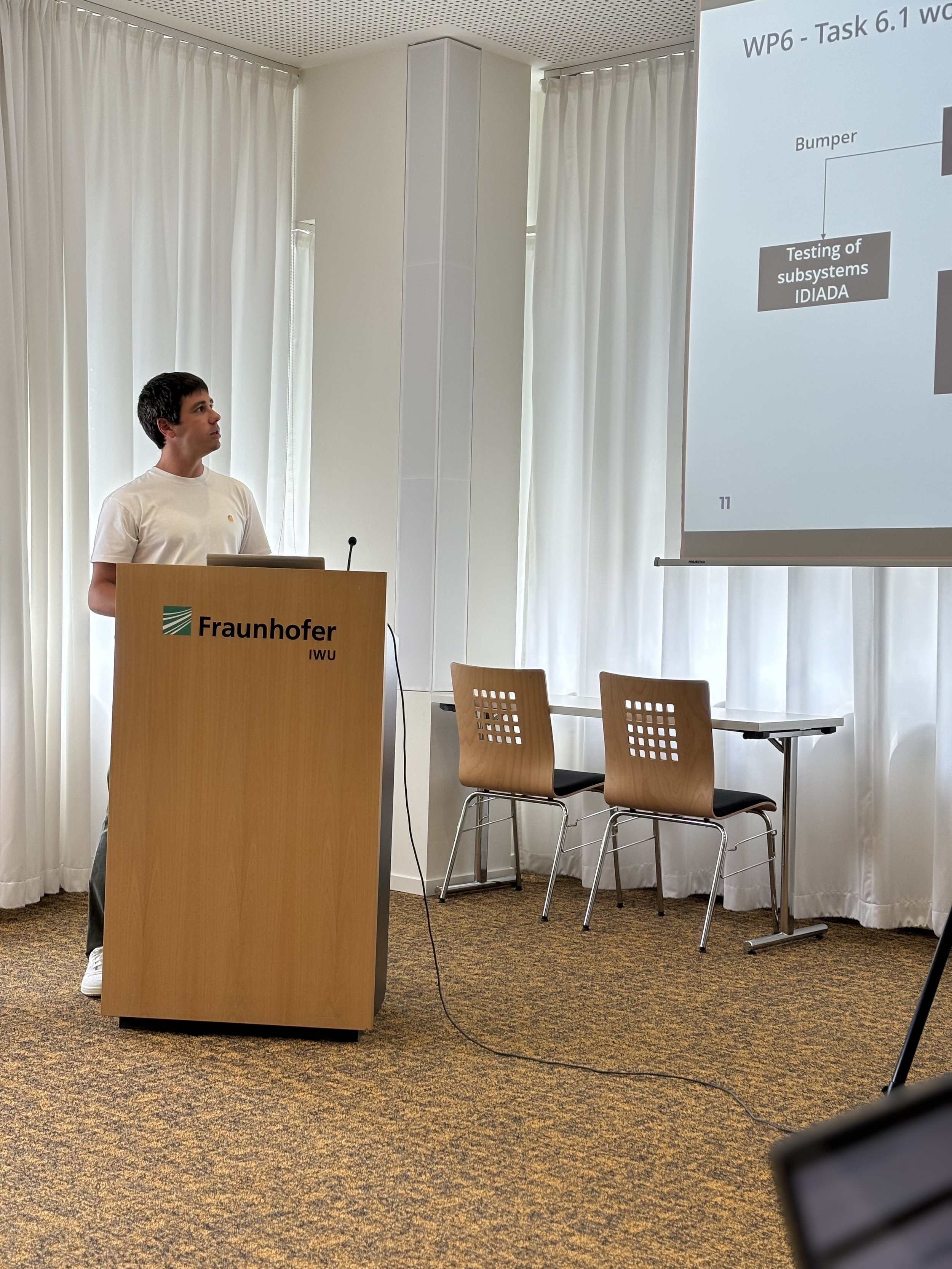
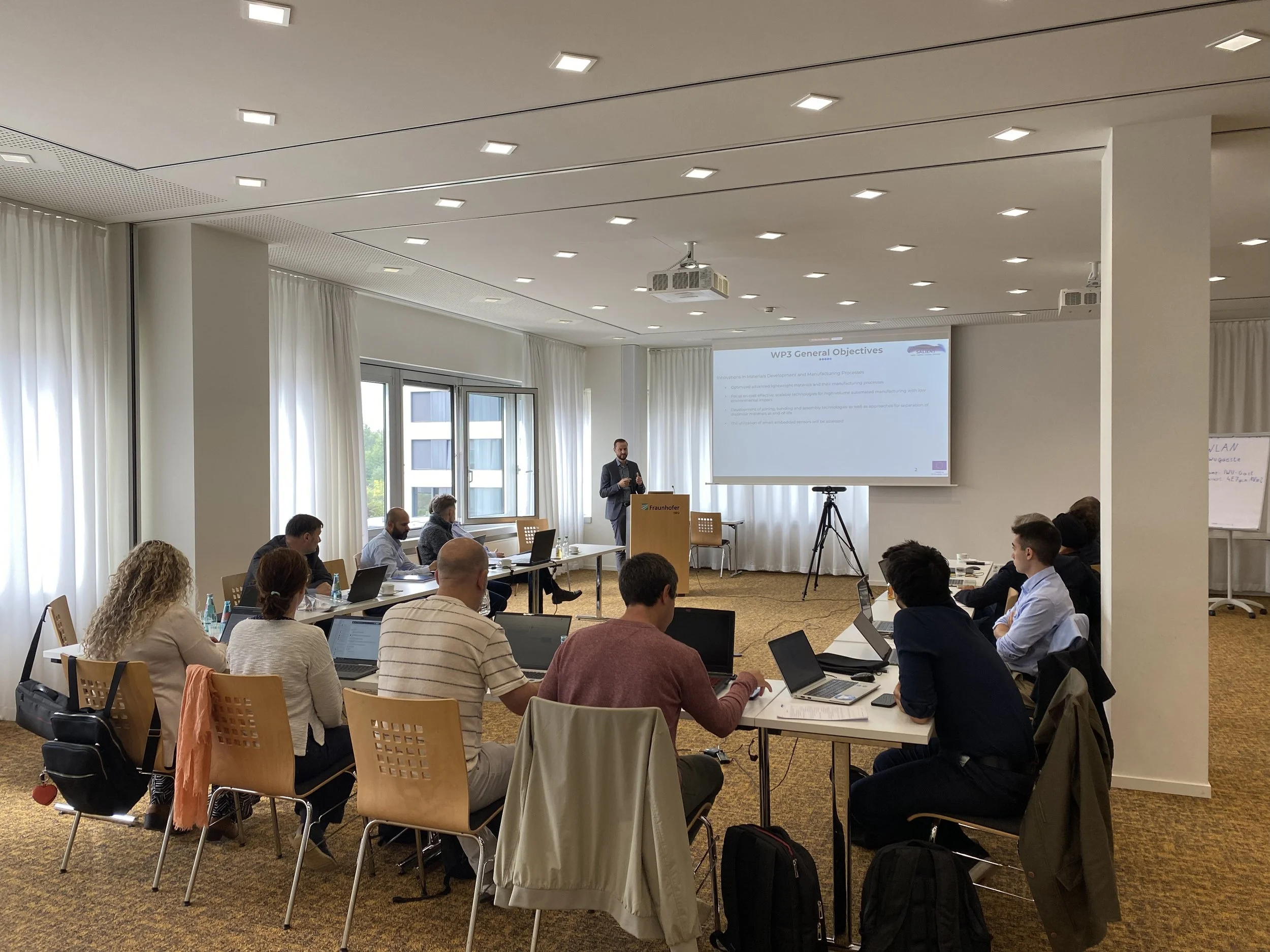
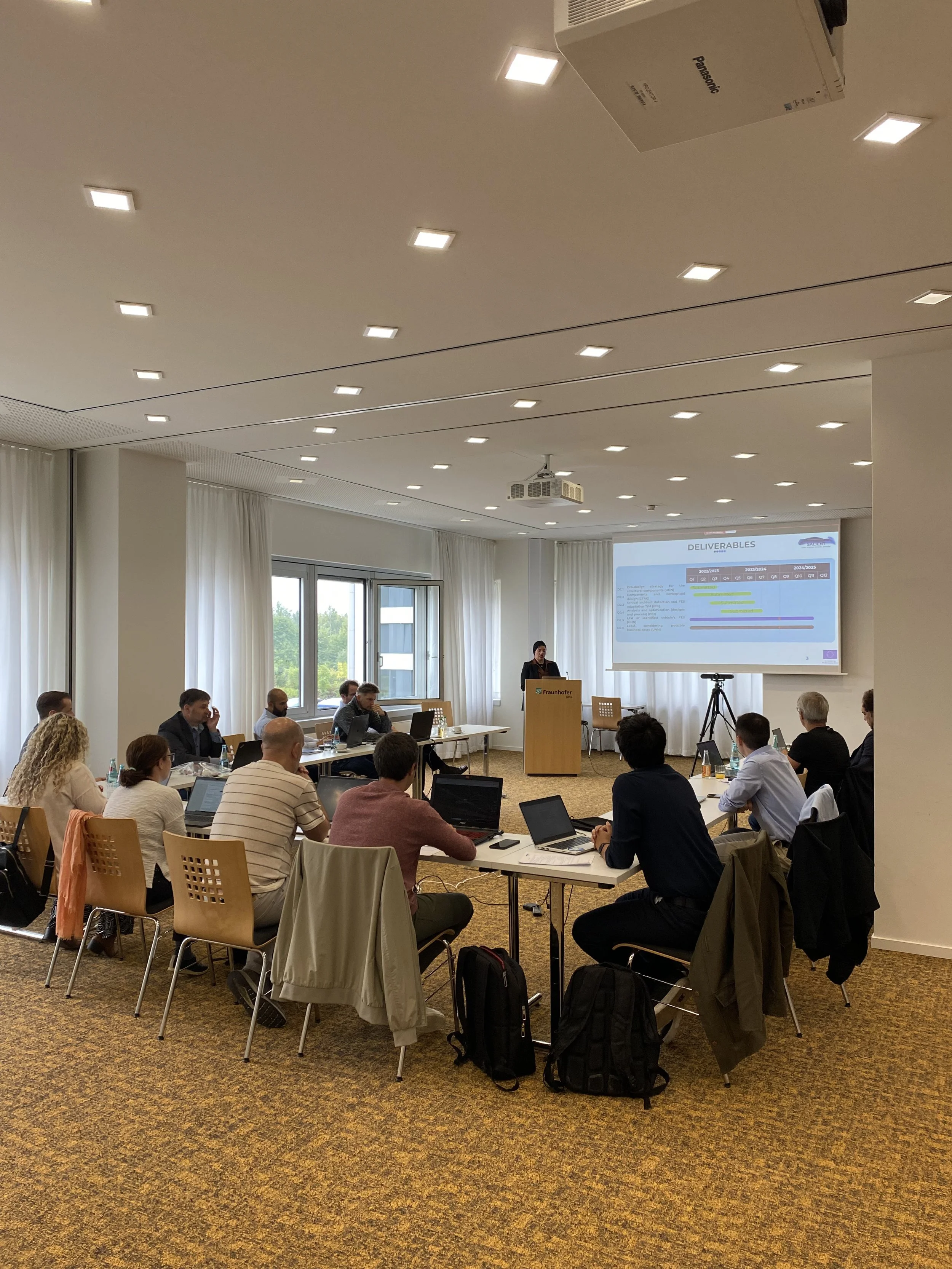